UG@60: Ugandan makes chicken incubators
Oct 14, 2022
A Ugandan who developed an idea to make his own incubator in 1988, says it worked so well that he took it for display at the Jinja annual agricultural show, attracting many orders for more.
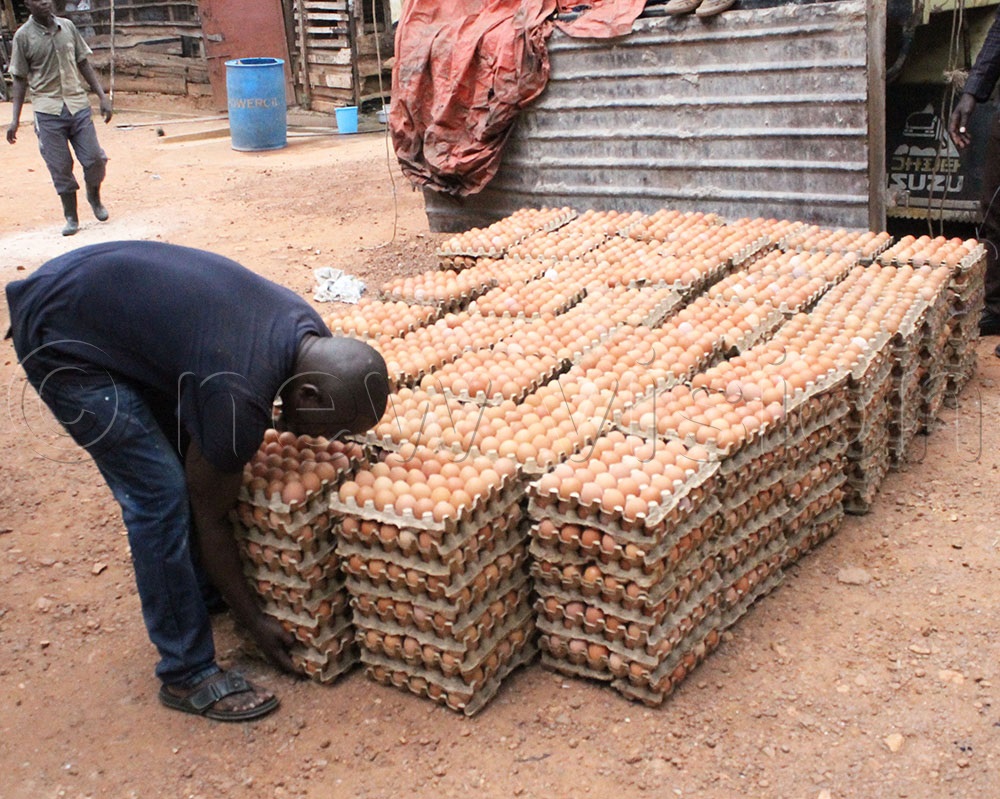
UG@60: Ugandan makes chicken incubators
NewVision Reporter
Journalist @NewVision
As Uganda celebrates her 60th independence, New Vision has been highlighting innovations, inventions and discoveries that Uganda has availed to her people and the world. Today, Herbert Musoke writes about Godfrey Walusimbi Kasolo, a farmer who innovated a better and bigger egg incubator that has become popular in the region.
A Ugandan who developed an idea to make his own incubator in 1988, says it worked so well that he took it for display at the Jinja annual agricultural show, attracting many orders for more.
Now, not only does he supply to many farmers in the country, but has also made incubators for Rwanda, DR Congo, Burundi and South Sudan.
In 1988, Kasolo ventured into poultry farming under his Butenga Poultry Farm in Kira division, Wakiso district.
A few years later, the farm grew to a respectable commercial level and he wanted to acquire an incubator and a hatchery to start producing his own chicks because of the delays and the poor quality day-old chicks some companies would supply.
“However, I realised that importing an incubator would be too expensive for me. So, in early 2000s, I decided to find ways of making one for myself. In 2005, we produced the first incubator for our farm,” he explains.
In the same year, Kasolo produced another one, which he took to the annual agricultural show in Jinja and that year, Butenga Farm was not only declared the best exhibitor, but also the best innovator at the show.
“The farmers fell in love with the incubator and immediately started placing orders to have it on their farms. Our innovation has eased chicken breeding in Uganda. A number of farmers are currently breeding their own chicks using our incubators,” he says.
Kasolo explains that breeding is more profitable than selling eggs.
Kisakye Sseggayi, a technician at Butenga Farm, says it is a way of adding value to eggs.
“A tray has 30 eggs and goes for between sh8,000 and sh10,000 farm-gate price, yet a day-old chick goes for sh2,500 (broilers) and sh4,500-sh5,000 for layers. Hatching an egg would cost up to sh500. We now have a hatchery arm of the farm called Butenga Farmers Chick Star,” Sseggayi says.
He adds that, therefore, from the 30 eggs of broilers, one would earn sh75,000. When you deduct sh6,000 for hatching, you earn sh69,000. For layers, you earn sh135,000. When you deduct sh6,000 for hatching, you earn sh129,000 from just one tray.
“However, the hatching rate depends greatly on the best agronomical practices at the parent stock farm, including the quality of the birds, feeding, health and hento-cock stock ratio, in addition to the way a farmer handles the eggs,” he explains.
This venture is profitable because the demand for day-old chicks is increasing each day as more people join poultry farming.
Making a hatchery
To make hatcheries, Kasolo got a team of well-trained engineers, carpenters and metal workers, who came together to produce what has now become one of the most widely used incubators and hatcheries in Uganda.
“Much of the material used is electrical-related, including switches and heat-controlling capsules. Also, we have whiteboards and pine wood. We use pine because it is light and is not commonly attacked by wood pests,” he explains.
Kasolo adds that inside the box are trays on which eggs are placed. Each tray accommodates 140 eggs and for the small incubators that take 860 eggs, there are seven trays.
The number of trays differs with the size of the incubator, ranging from over 30 tray-capacity (3,360 eggs) to 90 trays (10,089 eggs) and above.
“The gaps in the trays are created in rationality with the biggest egg. If you don’t think about the egg-size while constructing the trays, you will go wrong,” Kasolo explains.
He adds that all incubators use single-phase power. He, however, advises farmers to always have a standby generator that is automatically switched on when grid power goes off. This is because if power goes off without a standby generator, eggs will get spoilt and chicks will die within.
“Eggs are put into the incubator for 18 ½ days. They are candled after 12 days (eggs are passed over a candle to sort out the unfertilised ones, which are transparent).
“The condition in the incubators allows the chicks to develop and grow in the egg and, therefore, the unfertilised will be transparent. Later, they are taken to the hatchery for 2½ days to make 21 days, just like the hen does, Kasolo explains.
Affordability
Kasolo explains that the largest incubator from Butenga, with a capacity of 10,080 eggs, costs sh15m compared to a similar imported one that goes for about $20,000 (sh70m).
“We have experts to assemble it for you at the site,” he adds.
“The smallest capacity incubator of 860 eggs costs about sh4.5m. There are different capacities of 3,360 eggs and 6,800 that cost between sh8m and sh10m. These incubators can last for years if managed well,” Kasolo says.
He adds that most of the orders come from Uganda, but currently, they have orders from Rwanda, DR Congo, Burundi and South Sudan.
Kasolo notes that they can arrange easy payment terms as long as a customer pays 50% of the cost of the incubator upfront.
“Our biggest challenge is the rising cost of materials used in the construction of incubators, especially the imported material, such as whiteboards that work as a flame and electrical gadgets. Some we can get locally, such as pine wood,” he says.
No Comment